Working Principle
Air-cooled chillers directly dissipate heat into the air through the air-cooled condenser. These chillers are ideal for areas with water shortages or where water supply is inconvenient.
As shown in the air-cooled chiller operation diagram, the cooling process follows a closed-loop cycle:
- Evaporation: The refrigerant absorbs heat from the cooled object (e.g., chilled water) in the evaporator and vaporizes.
- Compression: The compressor extracts and compresses the refrigerant vapor into high-temperature, high-pressure gas.
- Condensation: The refrigerant gas enters the condenser, where it releases heat into the air and turns into a liquid.
- Expansion: The liquid refrigerant passes through the expansion valve, reducing pressure before entering the evaporator.
- Repeat cycle: The refrigerant re-vaporizes, absorbs heat, and the cycle continues.
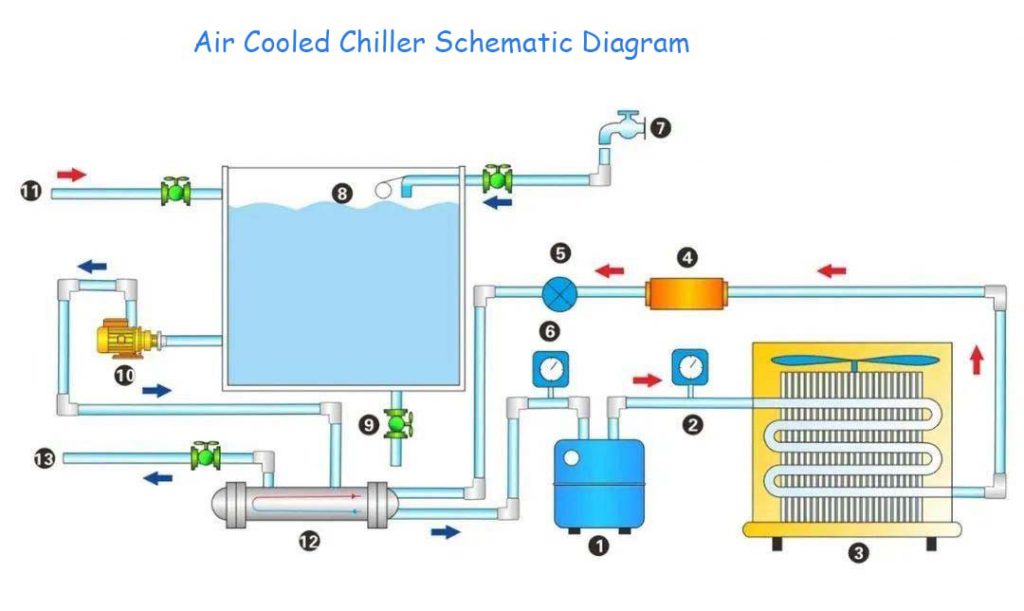
Key Features of Air-Cooled Chillers
- Uses finned condensers with fans for heat dissipation, eliminating the need for cooling towers, cooling water pumps, or cooling pipelines.
- Easier installation compared to water-cooled chillers, especially for small-capacity units that require mobility.
- Higher condensation temperature than water-cooled chillers, leading to slightly higher power consumption.
- Avoids issues like scale buildup or water pipe blockages in regions with poor water quality, while saving water.
- Finned condensers require regular cleaning to maintain heat exchange efficiency.
Applications
Air-cooled chillers are widely used in:
🏥 Pharmaceuticals & laboratories
🧪 Chemical processing
🍔 Food & beverage production
🛢 Oils & coatings
🛠 Electroplating & machinery processing
🏢 HVAC & commercial buildings
🖨 Plastics, fiber, and laser cooling
Comparison: Air-Cooled vs. Water-Cooled Chillers
Feature | Air-Cooled Chiller | Water-Cooled Chiller |
---|---|---|
Size | Smaller, compact | Larger due to cooling towers |
Efficiency | Lower (higher power consumption) | Higher efficiency |
Water Usage | No water required | Requires a steady water supply |
Maintenance | Simple, easy to maintain | Requires cleaning & water treatment |
Installation Cost | Higher upfront cost but no cooling tower | Lower unit cost but needs extra infrastructure |
Best Use Cases | Areas with water shortages or space constraints | Large facilities with stable water supply |
Installation Considerations
1. Distance to Temperature-Controlled Equipment
- Shorter distances reduce pressure drop and cooling loss in pipelines.
- Makes operation easier if there is no remote control function.
2. Noise Impact
- Major noise sources: compressor, circulation pump, and fans (fans are the loudest).
- Small chillers (~65 dB(A)) can be installed indoors.
- Large units (above 20HP) should be placed outdoors or away from workspaces.
3. Water Supply & Drainage
- Automatic refill sources should be available for maintenance.
- If using manual refilling, only drainage needs to be considered.
4. Installation Environment
- Outdoor installation is preferred for better heat dissipation.
- Outdoor chillers have weatherproof designs but are more expensive.
- Remote control access for monitoring and troubleshooting is recommended.
Working Principle and Features of Air-Cooled Chillers