Chillers play a crucial role in industrial cooling, HVAC systems, and commercial spaces. Whether in shopping malls, manufacturing plants, or data centers, chillers provide essential temperature control. But with multiple types and configurations available, how do you choose the right one? This guide breaks down chiller types, key selection factors, and industry-specific recommendations.
1. Understanding Chiller Types
1) Air-Cooled vs. Water-Cooled Chillers
Chillers are categorized based on their cooling method:
โ Air-Cooled Chillers
- Use finned heat exchangers and fans to dissipate heat into the air.
- Compact design with no need for cooling towers.
- Ideal for smaller cooling loads and space-limited environments.
- Common applications: Small commercial spaces, villas, and low-capacity cooling needs.
- Limitations: More sensitive to ambient temperature changes, lower efficiency in hot climates.
โ Water-Cooled Chillers
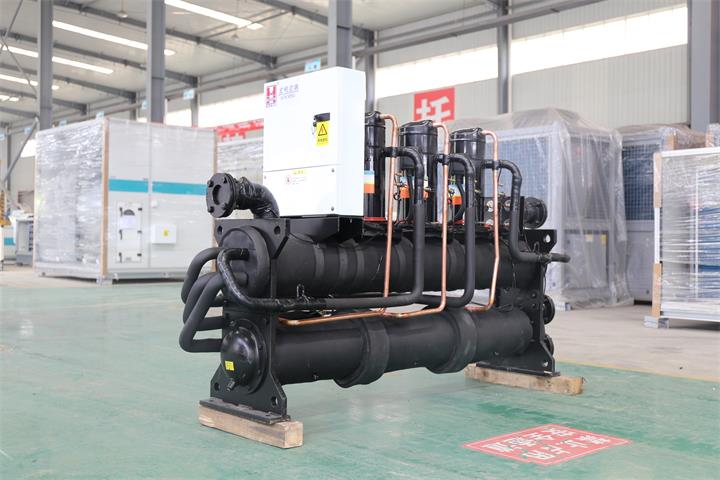
- Use water and cooling towers to reject heat efficiently.
- More stable performance, higher cooling capacity, and better energy efficiency.
- Common applications: Large-scale industrial plants, shopping malls, and manufacturing facilities.
- Limitations: Requires additional infrastructure (cooling towers, pumps, piping).
๐น Key Takeaway: Choose air-cooled chillers for small-scale cooling and space-constrained locations. Water-cooled chillers are better for large-capacity, high-efficiency cooling needs.
2) Chiller Types Based on Compressor Technology
Different chillers use different compressor technologies, impacting performance, cost, and efficiency.
Chiller Type | Compressor Type | Cooling Capacity | Best For |
---|---|---|---|
Scroll Chiller | Scroll Compressor | Small (0.2โ15P) | Small offices, commercial spaces |
Screw Chiller | Screw Compressor | Medium (30Pโ2000KW) | Industrial cooling, large HVAC |
Centrifugal Chiller | Centrifugal Compressor | Large (1000KW+) | Large-scale cooling, power plants |
Magnetic Bearing Chiller | Magnetic Levitation Compressor | High Efficiency (1000KW+) | High-tech facilities, data centers |
โ Scroll Chillers
- Small-capacity chillers with a compact design.
- Uses multiple scroll compressors for flexibility.
- Ideal for small-to-medium cooling applications.
โ Screw Chillers
- Higher cooling capacity (30P and above).
- More stable and efficient for large-scale industrial cooling.
- Common applications: Large factories, production lines, commercial buildings.
โ Centrifugal Chillers
- Best for very high cooling loads (1000KW+).
- Uses a high-speed centrifugal compressor.
- Common applications: Power plants, chemical processing plants, and large-scale industrial applications.
โ Magnetic Bearing Centrifugal Chillers (Most Advanced)
- Uses oil-free, frictionless compressors for higher efficiency and lower noise.
- Energy savings of up to 40% compared to traditional centrifugal chillers.
- Best for data centers, hospitals, and high-tech manufacturing facilities.
- Limitation: Requires large cooling loads (1000KW+) for cost-effectiveness.
๐น Key Takeaway: Scroll chillers are cost-effective for small applications, while screw and centrifugal chillers are ideal for large-scale cooling. Magnetic bearing chillers are the most energy-efficient but require high cooling loads.
2. Key Factors to Consider When Choosing a Chiller
1) Cooling Load & Capacity Requirements
- Determine the required cooling capacity (in kW or RT) based on the building or process needs.
- Choose a chiller that matches your peak and partial load conditions.
2) Energy Efficiency & Operating Costs
- Look for high-efficiency models (e.g., magnetic bearing chillers) to reduce energy consumption.
- Consider COP (Coefficient of Performance) and IPLV (Integrated Part Load Value) ratings.
- Higher efficiency = lower long-term operating costs.
3) Available Space & Installation Requirements
- Air-cooled chillers are more compact but require proper airflow.
- Water-cooled chillers need extra space for cooling towers and piping infrastructure.
4) Climate & Environmental Factors
- Hot climates: Water-cooled chillers perform better in high ambient temperatures.
- Water-scarce regions: Air-cooled chillers avoid water dependency.
- Noise restrictions: Magnetic bearing chillers have lower operational noise levels.
5) Maintenance & Longevity
- Oil-free systems (magnetic bearing) require less maintenance.
- Water-cooled systems need regular water treatment to prevent scaling.
- Ensure availability of spare parts and technical support.
3. Industry-Specific Recommendations
Industry | Recommended Chiller | Why? |
---|---|---|
Commercial Buildings & Offices | Scroll or Screw Chillers | Flexible capacity, compact, cost-effective |
Manufacturing & Industrial Processes | Screw or Centrifugal Chillers | High cooling loads, energy-efficient |
Data Centers & High-Tech Facilities | Magnetic Bearing Chillers | High efficiency, low noise, oil-free |
Power Plants & Chemical Processing | Centrifugal Chillers | Handles extremely large cooling demands |
Hospitals & Laboratories | Water-Cooled Screw or Magnetic Chillers | Precise temperature control, reliability |
Conclusion
Choosing the right chiller system depends on:
โ Cooling capacity requirements
โ Energy efficiency goals
โ Space limitations and infrastructure
โ Industry-specific cooling needs
๐น For small-to-medium applications, scroll or screw chillers offer flexibility.
๐น For high-capacity industrial cooling, centrifugal chillers are ideal.
๐น For the highest efficiency, magnetic bearing chillers provide the best long-term savings.
Selecting the right chiller ensures optimal cooling performance, lower energy costs, and long-term reliability. ๐