Commercial and Industrial Chiller Manufacturers
HON MING TECHNOLOGY GROUP (formerly HON MING Kangming International, a Sino-foreign joint venture headquartered in Guangzhou) was founded in 1993. The company integrates research and development, manufacturing, sales, testing, and services, with products widely used in air purification handling units, refrigeration (heating) chillers and terminal units, HVAC, and industrial cooling systems. It provides high-efficiency, stable, and energy-saving customized solutions for global HVAC and industrial users.
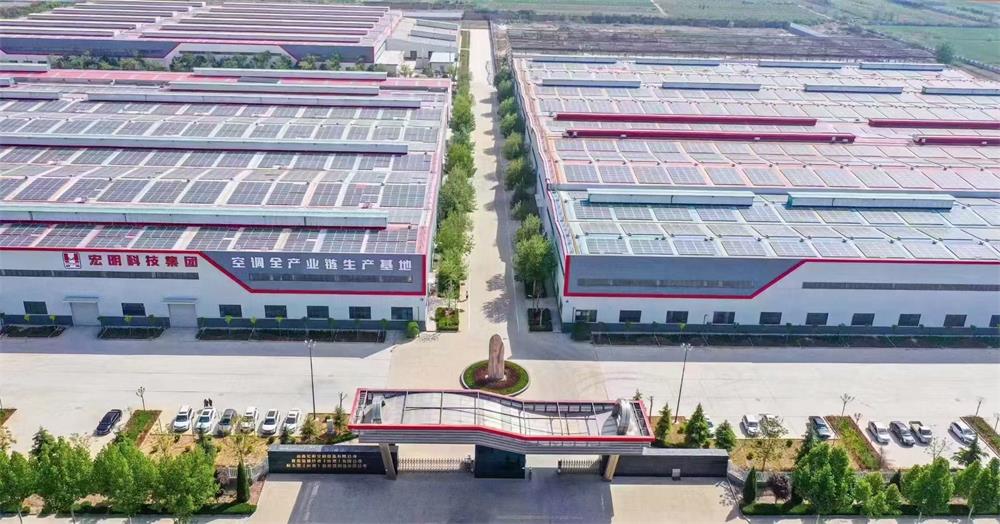
Adhering to the whole-industry-chain development concept, HON MING TECHNOLOGY GROUP is committed to building a diversified intelligent industrial park, offering customers stable products, advanced technology, and efficient comprehensive application solutions. The company has over 500 employees and collaborates with universities in China to cultivate talent for the design and production of air conditioning and cooling tower equipment. Additionally, it boasts a professional installation team and after-sales maintenance service team, continuously improving product technology and service capabilities.
Our main products include industrial chillers, industrial oil coolers, industrial air coolers, screw chillers, air-cooled chillers, water-cooled chillers, constant temperature chillers, dual-purpose heating and cooling units, explosion-proof chillers, and low-temperature chillers.
Hon Ming, Your Trusted Commercial Chiller Supplier
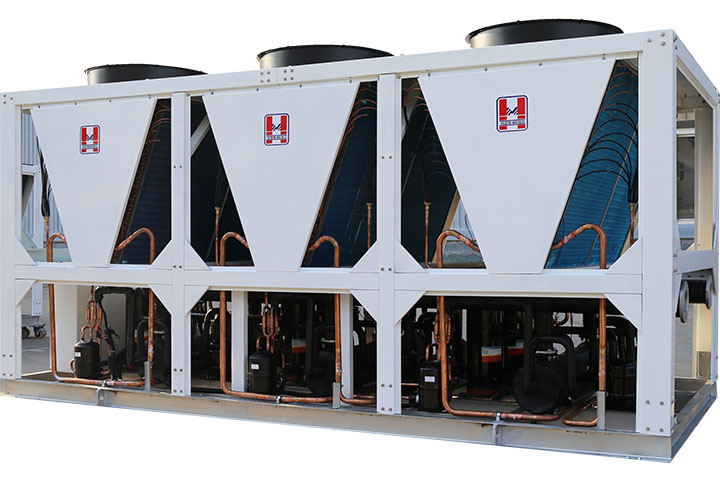
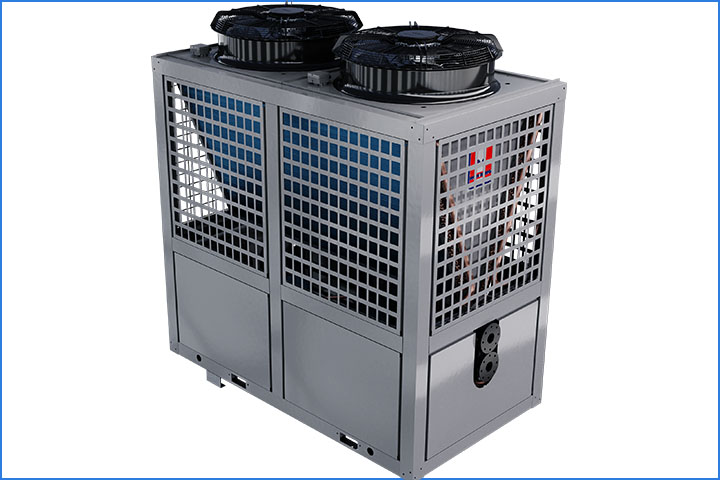
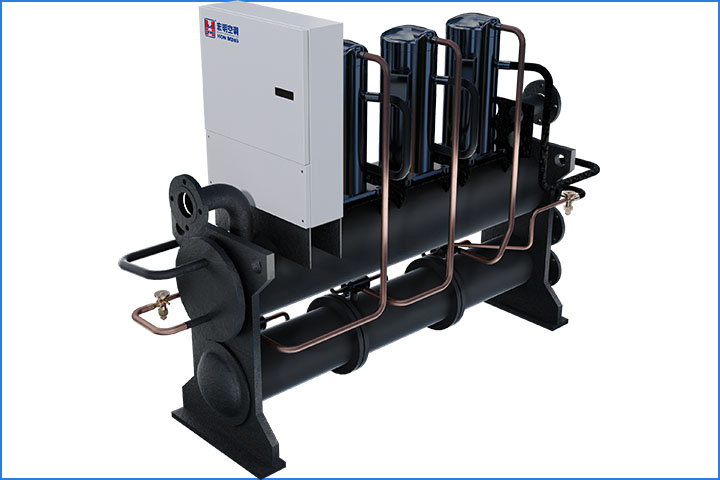
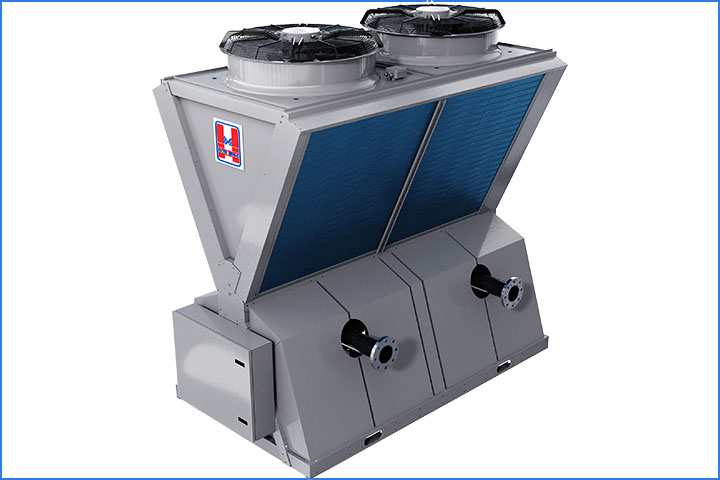
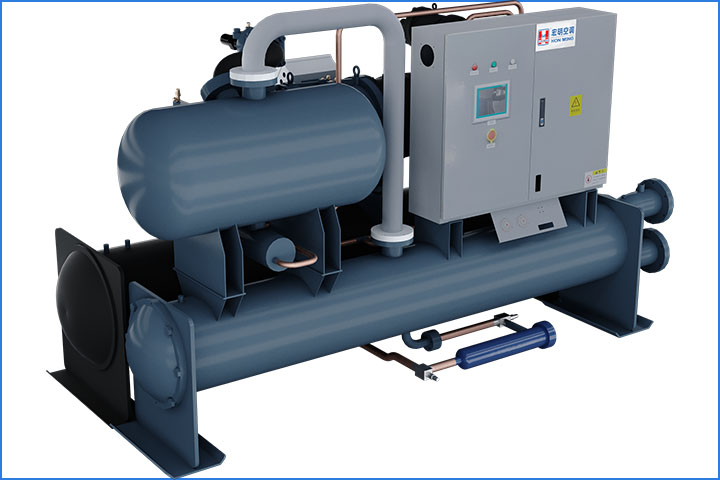
Working Principle and Process of Chillers
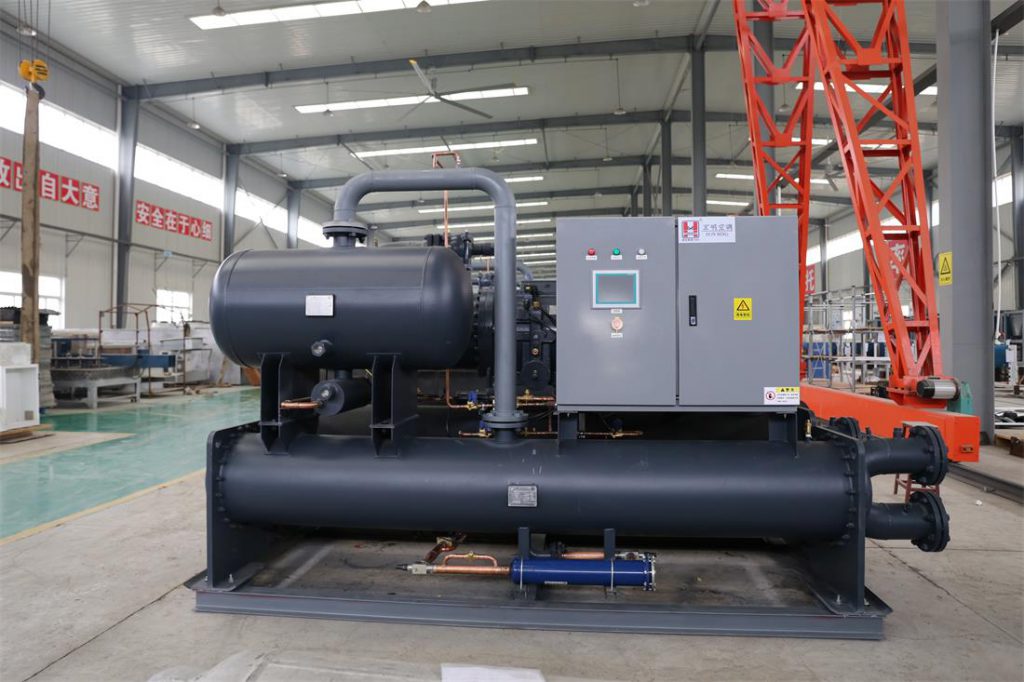
The working principle of a chiller is based on the vapor compression refrigeration cycle, which can be summarized as follows:
- Compression Process: The compressor, acting as the heart of the chiller system, compresses the low-temperature, low-pressure refrigerant gas into a high-temperature, high-pressure gas. This increases the refrigerant’s temperature and pressure, preparing it for heat release.
- Heat Exchange (Condensation): The high-temperature, high-pressure refrigerant gas enters the condenser, where it releases heat through contact with a cooling medium (such as water or air). As a result, the refrigerant condenses into a high-pressure liquid. The heat carried away by the cooling medium is usually discharged into the external environment.
- Throttling Process: The high-pressure liquid refrigerant from the condenser passes through an expansion valve or throttling device, where its pressure drops sharply, leading to a decrease in temperature. This transforms it into a low-temperature, low-pressure liquid.
- Evaporation Process: The low-temperature, low-pressure liquid refrigerant enters the evaporator, where it absorbs heat from the medium being cooled (usually water). This heat absorption causes the refrigerant to evaporate into a gas. As a result, the chilled water supplied by the chiller reaches the desired temperature for cooling applications.
- Continuous Cycle: The low-temperature, low-pressure refrigerant gas generated in the evaporator is then drawn back into the compressor, where the cycle begins again. This continuous cycle of heat absorption and release maintains the chiller’s cooling effect.
Throughout this process, the refrigerant circulates within a closed system, undergoing phase changes between gas and liquid to transfer heat effectively. The efficiency and performance of a chiller depend on the coordination of its components, the choice of refrigerant, and the optimization of the system’s design. In industrial applications, chillers precisely regulate cooling water temperature to ensure stable equipment operation and high production efficiency.
Types of Chillers
Chillers can be categorized based on cooling method, compressor type, and application. The main types include:
1. Based on Cooling Method
- Air-Cooled Chiller: Uses air to dissipate heat through fans and a condenser. Suitable for areas with limited water resources and easier to install but slightly less efficient than water-cooled models.
- Water-Cooled Chiller: Uses water as the cooling medium, requiring a cooling tower for heat dissipation. More efficient than air-cooled chillers and ideal for large-scale industrial applications.
2. Based on Compressor Type
- Screw Chiller: Equipped with a screw compressor, suitable for medium to large cooling capacities. Known for high efficiency and stable performance.
- Scroll Chiller: Uses scroll compressors, offering lower noise and high reliability, ideal for small to medium-sized applications.
- Centrifugal Chiller: Uses centrifugal compressors for large cooling loads, commonly used in commercial and industrial facilities requiring high capacity.
- Reciprocating Chiller: Features a piston-based reciprocating compressor, suitable for smaller cooling capacities with moderate efficiency.
3. Based on Temperature and Special Functions
- Constant Temperature Chiller: Maintains precise cooling temperature, widely used in laboratories and precision manufacturing.
- Low-Temperature Chiller: Provides ultra-low cooling temperatures, often used in pharmaceutical, chemical, and food industries.
- Explosion-Proof Chiller: Designed for hazardous environments where flammable gases or chemicals are present.
- Dual-Purpose Heating and Cooling Chiller: Can operate in both cooling and heating modes, improving energy efficiency in HVAC systems.
Each type of chiller is designed to meet specific operational needs, ensuring efficient cooling, energy savings, and system stability in various industries.
How to Choose the Right Chiller
Selecting the right chiller depends on cooling requirements, operating conditions, and application-specific needs. Here are the key factors to consider:
1. Cooling Capacity
- Determine the required cooling load (kW or tons of refrigeration) based on your application.
- Ensure the chiller’s capacity meets or slightly exceeds the heat load to maintain stable operation.
2. Chiller Type
- Air-Cooled Chiller: Suitable for locations with limited water supply and easy to install.
- Water-Cooled Chiller: Offers higher efficiency but requires a cooling tower and water circulation system.
3. Temperature Requirements
- Standard chillers maintain moderate cooling (5–20°C).
- Low-temperature chillers are needed for applications requiring temperatures below 0°C (e.g., pharmaceuticals, chemical processing).
- Constant temperature chillers provide precise cooling for sensitive equipment.
4. Compressor Type
- Scroll compressors: Energy-efficient and suitable for small to medium cooling needs.
- Screw compressors: Ideal for medium to large applications with high stability.
- Centrifugal compressors: Best for large-scale industrial or commercial cooling systems.
- Reciprocating compressors: Suitable for small systems but less efficient.
5. Energy Efficiency
- Look for high COP (Coefficient of Performance) or EER (Energy Efficiency Ratio) to reduce power consumption.
- Consider variable-speed drives (VSD/VFD) for better energy savings in variable load conditions.
6. Environmental and Safety Requirements
- Choose refrigerants with low global warming potential (GWP) and ozone depletion potential (ODP).
- Explosion-proof chillers are necessary for hazardous environments with flammable gases.
7. Installation and Maintenance
- Ensure the available space supports the chiller’s size and weight.
- Consider maintenance ease, including filter cleaning, refrigerant refilling, and component accessibility.
8. Budget and Long-Term Costs
- Balance initial investment vs. operating costs (energy consumption, maintenance, and lifespan).
- A slightly higher upfront investment in an efficient, durable chiller can lead to significant long-term savings.
By carefully evaluating these factors, you can choose a cost-effective, efficient, and reliable chiller tailored to your industry’s needs.
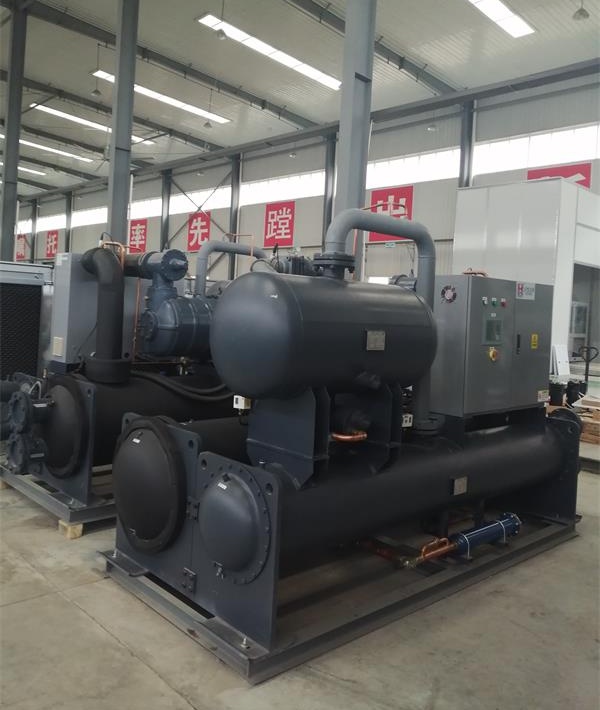